Surface topology air gap reluctance sensors (STARS) technology provides a needle change in terms of indication origin awareness and classification – determining an indication’s origin has never been more reliable or easier. Far gone are the laborious, error-prone days where operators were expected to get on their hands and knees to prove-up indication origins. STARS is an Eddyfi Technologies’ proprietary, patented technology that confirms indication surface origin with clarity and confidence. Furthermore, decisions can be verified via analysis of the accompanying STARS image to provide yet further confidence… what seems so simple really is.
The industry, having recognized the true potential of STARS, demanded an increased emphasis which was met via the introduction of the FloormapX, and the accompanying data analysis and management reporting software suite SIMS™ PRO. The FloormapX harnesses both advanced magnetic flux leakage (MFL) and STARS technology harmoniously into one state-of-the-art tank floor inspection tool. SIMS PRO delivers smart analysis capabilities that allow origin verification, classification, and remote decisions to be taken with confidence. Eddyfi Technologies has provided the most efficient total tank floor solution necessary to deliver the detection, data analysis and decision confidence that both inspection companies and asset owners seek.
Capability of STARS
So why the fuss? Well today, via the FloormapX and SIMS PRO, not only can STARS improve MFL sizing accuracy (the amplitude of an MFL signal from a top-side defect is different from the bottom side; this helps reduce this ambiguity), but this tool also provides a remarkably detailed, nearly photographic-quality map showing the top surface profile—even through thick coating up to 8 millimeters (0.31 inches). A typical example of STARS is shown below with the image of a sketch plate.
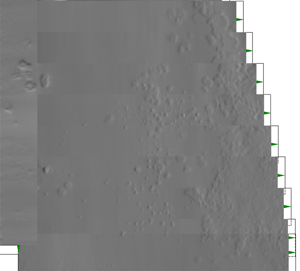
Figure 1 Multiple STARS scans through 3 millimeters (0.11 inches) of coating
But the capabilities do not stop there. STARS allows viewers to further classify indications as relevant or non-relevant, either in the tank or remotely via SIMS PRO. Via the STARS view, which is automatically presented to the FloormapX operator during data acquisition, we can identify protrusions on the plate surface such as weld spatter (Figure 2) and welds (Figure 3). We can also reveal existing repair plates undercoating (Figure 4). STARS can even identify undulations and buckling thus giving insights into tank settlement.
Figure 2 Protrusions caused by weld splatter
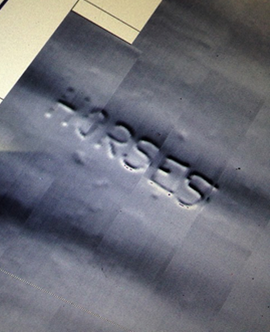
Figure 3 Weld lettering presented by STARS through a thick coating
![Square repair place identification through a thick coating [6+ millimeters (0.23 inches)]](https://blog.eddyfi.com/hs-fs/hubfs/Square%20repair%20plate%20identification%20through%20a%20thick%20coating%20%5B6+%20millimeters%20(0.23%20inches)%5D.png?width=300&name=Square%20repair%20plate%20identification%20through%20a%20thick%20coating%20%5B6+%20millimeters%20(0.23%20inches)%5D.png)
Figure 4 Square repair place identification through a thick coating [6+ millimeters (0.23 inches)]
Now that we understand the capabilities of STARS and its benefits, let’s take some time to understand how the technology works.
Demystifying STARS
Let us first take a close look at the magnet bridge and sensor arrangement.
Figure 5 Cross-section view of a magnet bridge and sensor positions
As seen in the image above, the horseshoe shape magnet bridge is suspended over the plate being inspected. The FloormapX itself includes two separate hall-effect sensor arrays, one for MFL array and the other for STARS, each with a resolution of 64-channels across the 300-millimeter (12-inch) width of the bridge. Hall-effect sensors are sensitive to magnetic fields that are perpendicular to their surface.
MFL sensors are located between the front and rear poles of the magnet to detect magnetic leakage fields caused by corrosion pitting from either the top or bottom surface of the plate. STARS sensors are mounted on the bottom surface of the rear magnet pole and are oriented to respond to top surface variation only.
But what exactly are our STARS sensors measuring?
Signals from MFL and STARS are shown in Figure 6 from a plate containing machined, semi-spherical defects with peak depths of 20%, 40%, 60%, and 80%.
Figure 6 MFL and corresponding STARS signals for bottom-side and top-side defects. STARS only has indications when defects are on the topside.
STARS works on the principle of air-gap reluctance. When scanning over areas with no product-side corrosion, the gap will remain mostly constant. The magnetic flux lines will travel vertically, taking the path of least reluctance between the pole and plate surface. They travel parallel to the STARS sensor, do not intersect it, and there is no response from STARS. This is illustrated in the left side image of Figure 6. We see a strong response from the MFL sensors, but no response from the STARS sensors. FloormapX decision = corrosion is on the bottom side.
A difference in air gap caused by product-side corrosion changes the reluctance of the magnetic path. The magnetic field lines take the shortest path, the path of least reluctance, and angle away from vertical towards the edges of the defect, intersecting the STARS sensor. This causes a STARS response as illustrated in the images on the right in Figure 6. We see a strong response from the MFL sensors, and we also see a strong response from STARS sensors. FloormapX decision = corrosion is on the top side. Sound complicated? It really isn’t.
The true beauty of STARS is that the technology does all the hard work for us, allowing the FloormapX to make simple, reliable top/bottom decisions while providing a beautiful, high-resolution image of the plate surface. The user does not need to do anything but look, no signal interpretation is required, indications are classified automatically and can be verified for complete confidence via the STARS image!
Figure 7 FloormapX data acquisition view: MFL on the left and STARS on the right
But this is only half the story. SIMS PRO data management and analysis reporting software provides the total solution by allowing us to analyze data captured by the powerful FloormapX and confirm decisions adding an extra unique level of confidence. SIMS PRO has been developed for the report creator to seamlessly ‘switch’ between the highest resolution C-scan images to confirm and classify indications meaning the confidence level in the report submitted is of the highest level. An example of this verification process can be seen in Figure 8 where the FloormapX has classified an indication as top surface, and SIMS PRO can be used to verify this finding.
Figure 8: Using SIMS PRO to verify surface origin of indications
In summary, STARS not only discriminates between product or soil-side corrosion, but it is also an invaluable and unique aid in determining whether an MFL signal is caused by loss of material or additional ferrous material such as a weld. This has a huge advantage of helping identify most ‘false calls’ found in MFL reports which are generated from the roughness or undulations on the plate surface. Being able to accurately visualize the surface and determine if MFL signals are from corrosion, buckling, or surface welds results in more accurate reports reaching the tank owner and minimizing unnecessary repairs.
We have some interesting plans for STARS in the near future, so subscribe to our blog for updates sent directly to your email to stay Beyond Current! Interested in discussing your next inspection campaign? Get in touch with our team of experts ready to help.
Authors: Matthew Kirkcough, Matthew Boat