Horton spheres are large pressure vessels that store hydrocarbons that are gaseous at room temperature —like butane, propane and natural gas— under such pressure that they remain in a liquid state. The spheres stand above ground on cylindrical steel legs. The legs are covered in fireproofing material, usually concrete, to prevent a failure in the case of a fire. The structural integrity of the legs is essential to ensure safety of the pressure vessel. Unfortunately, with water ingress and time, CUF may develop under the protective layer. Slowly working out of sight, the corrosion weakens the structural steel, compromising its integrity and potentially leading to dramatic consequences. Water ingress inside the support leads to corrosion with the same consequences but with even fewer visual clues.
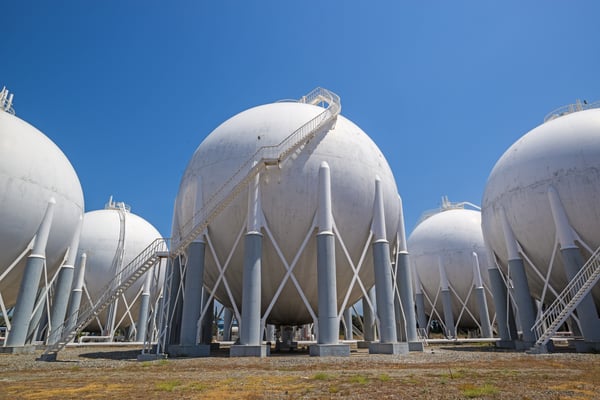
Figure 1: Horton Sphere Storage Tank
To prevent harmful failure, the sphere leg fireproofing must be inspected periodically. API 2218 and API RP 583 recommend surveying the fireproofing for cracking, bulging, or rust stains which are indicative of CUF. The standards recommend performing selective removal of the fireproofing to inspect the substrate and reinforcement. Unfortunately, CUF does not always display these signs. Reliability Engineer Kelly P. Caillier comments, “I have witnessed many areas where we found degradation was present, but no cracking, spalling, bulging, staining visually existed throughout the sphere leg.” Since the visible signs may not be present, “relying only on visual inspection can supply a false sense of security and end in a catastrophic event.”
To raise confidence, some asset owners will go to the extent of stripping the fireproofing at great expense to perform inspection on the bare steel. This procedure is effective but highly time consuming and very expensive. The following table presents a case study for the overall cost to inspect 10 legs of a sphere with stripping and replacement of the fireproofing.
-
Product: Propane
-
Sphere diameter: 19,000 mm (62.3 ft)
-
Number of legs: 10
-
Leg outside diameter: 700 mm (28 in)
-
Fireproofing thickness: 100 mm (4 in)
Type of inspection |
Scaffolding |
Fireproofing removal/Installation |
Inspection |
Typical repairs (USD) |
Total |
UT (stripped) |
$25,000 |
$260,000 |
$2,000 |
$30,000 |
$317,000 |
Table 1: Cost of UT inspection with concrete removal and installation
With a traditional inspection on the bare pipe, over 80% of the overall inspection cost comes from the stripping of the passive fireproofing layer prior to the inspection and the installation of a new passive protection after the inspection itself.
Pulsed eddy current has been used to inspect for CUF in spheres over the last decades with some success. PEC uses a magnetic pulse to induce eddy currents in the steel leg through liftoff. By measuring the decay of the eddy currents inside the component, the technology can compute an averaged wall thickness over the probe’s footprint. Unfortunately, older PEC technology was bound by limited productivity and capacity to detect small flaws.
The presence of carbon steel wire mesh or reinforcement bars in the concrete layer also posed problems because the response of the small interfering part is like that of a thinner wall thickness, potentially leading to false positives.
The Lyft® system introduced in 2016 reinvented PEC by enabling dynamic (continuous and encoded) acquisitions. Eddyfi Technologies designed the sensors and instrument to allow dynamic acquisition, moving away from traditional PEC sensor designs. This innovation doubled productivity capabilities. A smaller footprint compared to older PEC technology also allowed detection of smaller indications. In 2018, the introduction of the first Pulsed Eddy Current Array (PECA) probe with 6 channels and 457 millimeters (18 inches) of coverage changed the game by increasing productivity from five to tenfold on top of that! The introduction of these innovations is part of the Lyft DNA and our commitment to continually improve the capabilities of the system though software and hardware updates.
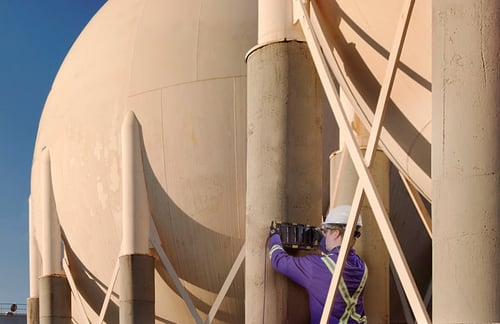
Figure 2: Sphere Legs Inspection with PECA
For Lyft owners who inspect sphere legs, it was a no-brainer when it came to integrating PECA in their inspections. Operators can deploy the probes either from scaffolding or rope access. Remotely deployed inspection is currently under study by Eddyfi Technologies.
To tackle the challenge of the wire mesh and rebar present in the fireproofing, we developed a special purpose algorithm that minimizes the risk of false positive due to interfering carbon steel components. This algorithm may be enabled on any Lyft system by checking the “Wiremesh/Reinforcement Bar” checkbox in the component definition prior to inspection.
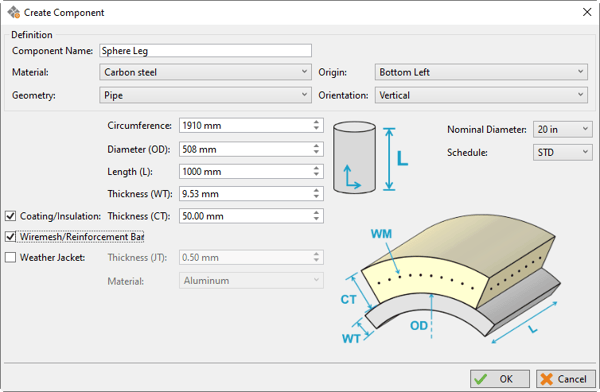
The remaining wall thickness sizing is available to the inspection team in real time. Once an area of corrosion is detected by PEC, the fireproofing is removed locally to perform further assessment of the indications.
Michaël Lemaire, NDT expert at Mistras, has overseen hundreds of sphere legs inspected with the Lyft system. His preferred inspection method is rope access deployment of PECA. He recommends that his clients use PECA to ensure a near 100% coverage. Kelly P. Caillier also prefers rope access deployment of PECA to inspect sphere legs. Increased productivity allows inspectors to perform higher resolution scans, increasing probability of detecting smaller flaws while minimizing the risk of false positives.
Figure 3: Rope Access Technician Scanning with PECA
PEC detects and assesses the extent of corrosion under the protective concrete layer. An inspection report can be provided to the client within a short time to assess if corrosion is present in the component. The inspection report is efficiently created in the SurfacePro 3D reporting software. This software allows users to add 3D models of the inspection data which offers the asset owner a better understanding of the assets at their facility.
Both collaborators agree that Lyft and PECA dramatically increase the level of confidence in their inspection results compared to a solely visual inspection or conventional PEC inspection of the sphere legs. Increased productivity enables improved resolution, better distinguished features and significantly reduced risk of false positives.
The following table presents the estimated overall project costs using different deployment scenarios. In one scenario, no damage is found; in the second one, typical CUF damage is found in localized areas of 50% of the legs; fireproofing being removed and reapplied only over areas of interest for PEC inspections is shown in the later scenario.
Type of inspection |
Scaffolding |
Fireproofing removal/Installation |
Inspection |
Typical repairs (USD) |
Total |
Scenario where no damage is found |
|||||
UT (stripped) |
$25,000 |
$260,000 |
$2,000 |
$0 |
$287,000 |
PEC (via scaffolding) |
$25,000 |
$0 |
$6,000 |
$0 |
$31,000 |
PEC (via rope access) |
$0 |
$0 |
$9,000 |
$0 |
$9,000 |
Scenario where typical localized CUF damage is found in 50% of the legs |
|||||
UT (stripped) |
$25,000 |
$260,000 |
$2,000 |
$30,000 |
$317,000 |
PEC (via scaffolding) |
$25,000 |
$30,000 |
$6,000 |
$30,000 |
$91,000 |
PEC (via rope access) |
$0 |
$30,000 |
$9,000 |
$40,000* |
$79,000 |
*Considering that scaffolding is erected on legs where damage is present
Whether damage is found or not, PEC provides significant cost savings over traditional inspection on the bare metal where most of the concrete is removed over areas where no damage exists. The overall project cost is also only marginally higher when using PEC compared to visual inspection without stripping but provides a much higher Probability of Detection (PoD) and confidence level.
Figure 4: SurfacePro 3D Model of the PEC Data
In this example, the PEC data shows an area of suspected corrosion. There was no visible cracking, bulging or rust stains in the concrete that would suggest damage. Local removal of the fireproofing exposed unequivocally the extent of the damage, as shown in the following picture. The 11mm (0.4in) thick steel leg was corroded to a through hole. Water was also found inside the structure, suggesting that corrosion worked its way from inside out of the structure.
Figure 5: Localized CUF Removal After Detection with PECA
If only a visual inspection of the concrete with selective removal of the fireproofing had been performed, this corrosion would have remained undetected. It would have kept growing, potentially leading to catastrophic consequences. Fortunately, Lyft and PECA enable near 100% coverage inspection without removal of the fireproofing. With periodic inspection, PEC ensures detection of flaws before they reach this extent of damage.
For more information on the Lyft for inspection of corrosion under fireproofing, visit here and contact our experts for answers to your specific questions today.